Introducción al marco legislativo
La seguridad y la evaluación de riesgos de máquinas en Europa está regulada por un conjunto de normativas y directivas destinadas a salvaguardar la protección de los trabajadores y de los consumidores frente a riesgos asociados al uso de máquinas y equipos. Estas regulaciones, enraizadas en el marco legal de la Unión Europea, se aplican uniformemente en todos los países miembros. Los fabricantes y otros actores de la cadena de suministro deben cumplir con las regulaciones y garantizar que sus productos cumplan con los estándares de seguridad establecidos en la Directiva de Máquinas y las normas armonizadas aplicables.Las principales regulaciones relacionadas con la seguridad y la evaluación de riesgos de máquinas Europa
Directiva de Máquinas (2006/42/CE)
Esta directiva establece los requisitos esenciales de seguridad y salud que deben cumplir las máquinas puestas en el mercado europeo. Define responsabilidades para fabricantes, importadores y distribuidores, y establece los procedimientos de evaluación de la conformidad de las máquinas.Normas armonizadas
La directiva de máquinas hace referencia a normas armonizadas que especifican los requisitos técnicos y de seguridad para diferentes tipos de máquinas. Estas normas son desarrolladas por organismos de normalización y proporcionan pautas detalladas para cumplir con los requisitos de la directiva. Además, existe una vigilancia del mercado. Las autoridades de los Estados miembros de la UE tienen la responsabilidad de llevar a cabo controles de mercado para asegurarse de que las máquinas cumplen con los requisitos de seguridad y salud. Las autoridades pueden tomar medidas, como retirar productos del mercado si no cumplen con los estándares. Para evitar consecuencias negativas en el negocio debido a una mala praxis, los fabricantes de maquinaria deben cumplir con los requisitos fundamentales de la Directiva de Máquinas:- Evaluación de riesgos: la directiva de máquinas requiere que los fabricantes realicen una evaluación de riesgos para sus máquinas y tomen medidas para eliminar o reducir los riesgos a un nivel aceptable. Esto implica el diseño de protecciones adecuadas, sistemas de control y documentación técnica.
- Marcado CE: las máquinas que cumplen con los requisitos de la directiva de máquinas deben llevar el marcado CE, que indica que cumplen con los estándares europeos de seguridad. Este marcado es obligatorio para las máquinas puestas en el mercado de la UE.
- Declaración de conformidad: antes de poner una máquina en el mercado, el fabricante debe emitir una declaración de conformidad que certifica que la máquina cumple con los requisitos de la directiva de máquinas.
- Expediente técnico: recopilación de planos, descripción completa de la máquina, relación de normas y especificaciones técnicas de referencia utilizadas, medidas de seguridad implementadas, relación de ensayos, controles de calidad y toda la documentación relacionada en la Directiva como a evaluación de riesgos o el certificado de conformidad.
La evaluación de riesgos
En primer lugar, hay que recordar que la declaración de conformidad (Certificado de Conformidad CE) es una autocertificación por la cual el fabricante asume la responsabilidad de que el producto que está comercializando, tras llevar a cabo un procedimiento de evaluación, cumple con los requisitos de seguridad y salud. Únicamente las máquinas incluidas en el Anexo IV de la Directiva requieren de una evaluación de la conformidad externa. Aunque pueda existir una creencia popular por la que el hecho de disponer de marcado CE y Certificado de Conformidad, una máquina ha pasado unos controles y es conforme, esto no es así. La máquina tiene una presunción de conformidad que no garantiza que cumple con la normativa de seguridad ni que haya pasado unos controles. De aquí la importancia que tiene la correcta realización de la evaluación de riesgos puesto que permite al fabricante encarar este proceso con garantías de cara a la responsabilidad que va a asumir. El problema que se encuentra el fabricante es que la metodología de evaluación de riesgos no está desarrollada en la Norma UNE-EN ISO 12.100:2010 (Seguridad de las máquinas. Principios generales para el diseño. Evaluación del riesgo y reducción del riesgo.). Es preciso ir al Informe Técnico ISO/TR 14121-2:2012 (Safety of machinery — Risk assessment — Part 2: Practical guidance and examples of methods) para encontrar las bases de un método a seguir. Es importante que la evaluación de riesgos se inicie en la fase inicial del proyecto, con el diseño, puesto que este se verá afectado por las medidas de seguridad a adoptar. Abordar la seguridad de la máquina cuando se ha terminado el diseño o incluso la fabricación, es un error muy común a evitar, por la dificultad de integrar las seguridades y el alto coste de las modificaciones en plazo y presupuesto. Vamos a ver ahora una de las metodologías que pueden utilizarse a la hora de llevar a cabo la evaluación de riesgos que, como hemos visto, es el primer escollo que se encuentra el fabricante y los técnicos encargados de la tarea.El método Hazard Rating Number (HRN)
El «Hazard Rating Number» (HRN) es el método específico de evaluación de riesgos de máquinas que utiliza CADE y que ya se aplica en entornos industriales. Este método se basa en asignar un número o puntuación a los peligros identificados en una máquina o proceso, lo que permite priorizar y tomar decisiones fundamentadas sobre las medidas de control necesarias. La metodología considera factores como la probabilidad de que ocurra el riesgo, la frecuencia de exposición al riesgo, el grado de los posibles daños y el número de personas en riesgo.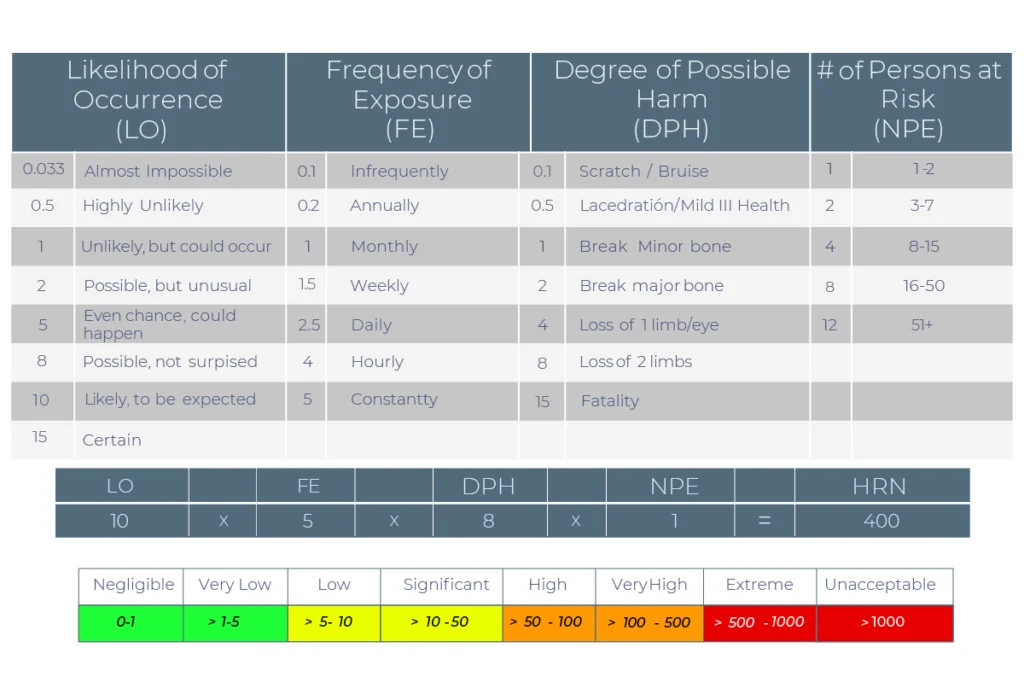
- Identificación de peligros: se realiza una revisión exhaustiva de la máquina o proceso para identificar todos los posibles peligros que puedan causar lesiones o daños a los trabajadores o al entorno.
- Asignación de puntuación al riesgo: cada peligro identificado se evalúa en función de diversos criterios, como la gravedad del daño potencial, la probabilidad de que ocurra y la exposición del trabajador al peligro. Estos criterios se ponderan y se asigna un número o puntuación al peligro.
- Priorización de riesgos: una vez que todos los peligros han sido evaluados y se les ha asignado un número de riesgo, se pueden priorizar en función de su puntuación. Los peligros puntuados más altos se consideran más críticos y requieren una atención prioritaria.
- Implementación de medidas de control: con base a la priorización de riesgos, se determinan las medidas de control necesarias para reducir o eliminar los peligros. Estas medidas pueden incluir el diseño de protecciones, el uso de equipos de seguridad, la capacitación de los trabajadores y otros controles preventivos.
- Reevaluación: la evaluación de riesgos debe ser un proceso continuo. A medida que se implementan medidas de control, es importante revisar y actualizar la evaluación de riesgos en caso de cambios en la máquina, el proceso o las condiciones de trabajo.
Las funciones de seguridad del sistema de control
Una evaluación de riesgos no puede considerarse completa si las medidas de seguridad adoptadas para algunos de los riesgos identificados están basadas en sistemas de control y, a su vez, estos se dejan sin análisis según alguna de las dos normas armonizadas que hay para tal fin. La más habitual en Europa es la Norma UNE-EN ISO 13849-1:2016 (Seguridad de las máquinas. Partes de los sistemas de mando relativas a la seguridad). Las funciones de seguridad del sistema de control (SRP/CS) de una máquina incluyen dispositivos tan comunes como las paradas de emergencia, puertas de acceso equipadas de detectores con o sin enclavamientos, barreras inmateriales y otros equipos ESPE (equipos de protección electrosensibles) o paradas seguras realizadas por programación. Todas estas medidas son parte habitual y de uso extendido de la seguridad de una máquina. Según esta norma, el análisis de riesgos preliminar proporciona un Nivel de Prestaciones o Rendimiento llamado en inglés Performance Level requerido (PLr) para la función de seguridad.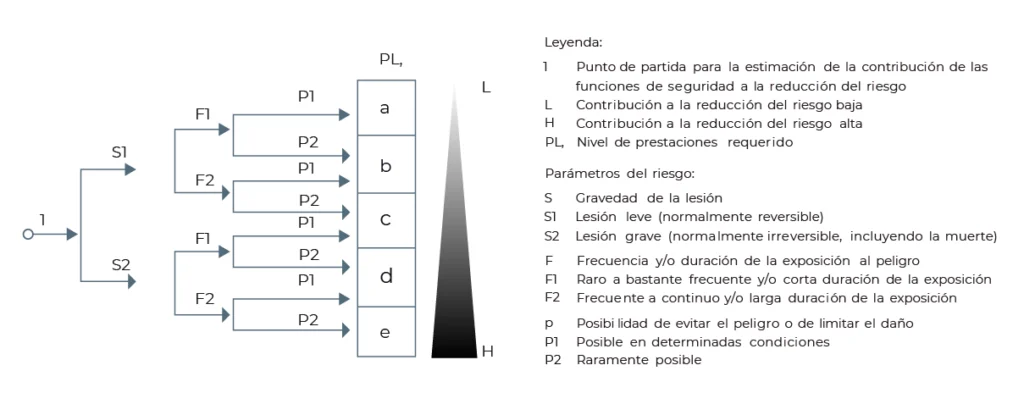
- La categoría de la arquitectura de control (canal simple, doble, etc.).
- El tiempo medio hasta el fallo (MTTF), que predice la fiabilidad y vida útil de los dispositivos.
- El grado de cobertura de diagnóstico (DC) es un patrón para la eficacia del diagnóstico.
- Los fallos por causa común (CCF) son los fallos de diferentes unidades a causa de un único incidente.
Resumen
La evaluación de riesgos es una obligación del fabricante de maquinaria según la Directiva Europea para asegurar la conformidad y poder asumir esta responsabilidad con garantías. Incluir la evaluación de riesgos en la fase inicial del diseño supone un ahorro de costes al reducir las modificaciones a la vez que evita retrasos en el plazo de entrega. La evaluación de riesgos requiere de una metodología objetiva y sólida como el HRN que permite establecer prioridades según la severidad de los riesgos para integrar las medidas de seguridad con éxito. El estudio del nivel de prestaciones o performance level de las funciones de seguridad del sistema de control es una parte esencial de la evaluación de riesgos de una máquina que no está completa sin este estudio. CADE realiza de manera habitual estas evaluaciones de riesgos tanto para los equipos que diseña y suministra como para las empresas clientes que solicitan este servicio. También se llevan a cabo certificaciones de producto, análisis de operatividad HAZOP, análisis de árboles de fallos FTA, análisis de modos de fallo FMEA, estudios ATEX, etc.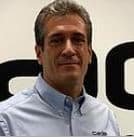
Artículo escrito por Carlos Martínez Peral