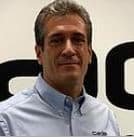
Artículo escrito por Carlos Martínez Peral
Si leíste el anterior artículo sobre el indicador OEE, ya habrás refrescado tus conocimientos sobre los orígenes del TPS de Toyota, así como del TPM y del Lean Manufacturing junto a su indicador estrella, el Overall Equipment Effectiveness o Eficiencia General de los Equipos.
De esta manera y dando continuidad a lo expuesto en el post anterior, es turno ahora de hablar del VSM, acrónimo de Value Stream Mapping o Mapa de Cadena de Valor, en su traducción al castellano.
¿Qué es el VSM?
El VSM es una representación gráfica de un proceso de producción mediante un diagrama de flujo con símbolos estandarizados de las diferentes actividades de trabajo, así como de los flujos de información, identificando los tiempos tanto de los pasos que aportan valor, como de los que no.
La importancia del VSM es clave para el Lean, ya que se trata de su herramienta de diagnóstico.
Hay otras herramientas importantes y muy conocidas que, aunque no vayamos a hablar sobre ellas en este artículo, cabe nombrarlas: 5S, Kamban, TPM y SMED, consideradas operativas; y otras herramientas de seguimiento como son la Gestión Visual y los KPI’s.
Tendremos ocasión de tratarlas con más detalle en futuras publicaciones.
Valor y desperdicio en Lean
Deberemos en primer lugar establecer el concepto de valor y relacionarlo de manera intrínseca con toda aquella actividad que tenga que ver con el proceso de producción de un producto, que permita asegurar sus funcionalidades y requisitos especificados, que asegure un nivel de calidad definido, y cumpla con un coste y plazo concreto. Todas estas cualidades y condiciones serán por las que el cliente estará dispuesto a pagar el precio acordado.
De esta manera, desperdicio (waste en inglés, muda en japonés) debe entenderse como toda actividad que NO aporta valor al producto o servicio porque consume recursos. Los siete desperdicios básicos según la metodología Lean son:
- Sobreproducción, producción de bienes antes de que sean requeridos por el proceso cliente.
- Tiempos de espera, recursos sin utilizar esperando a poder realizar una actividad.
- Transporte y almacenaje, tiempo invertido en transportar y almacenar materiales o documentos.
- Tiempos de proceso innecesarios, procesos ineficientes que originan la necesidad de realizar tareas sin valor añadido.
- Inventarios, acumulación de materia prima, producto en curso o terminado.
- Movimiento, cualquier movimiento que no es necesario para completar una operación de valor añadido.
- Defectos, uso o generación de productos que no cumplen las especificaciones.
Pero pueden considerarse otros, la falta de seguridad en los procesos, el desaprovechamiento de oportunidades o ideas de mejora o la no identificación de errores en fases tempranas de diseño, entre otros.
Empezando el mapeo
La primera tarea que se lleva a cabo es la de identificar la familia de productos que va a ser el sujeto del estudio VSM. Normalmente en la multiproducción, el 20% de las referencias suponen el 80% de la facturación, por lo que el estudio conviene iniciarlo analizando éstas.
A continuación debemos definir lo que se conoce como Cadena de Valor, que es una secuencia de actividades con aporte y sin aporte de valor, desarrolladas para conseguir un determinado producto o servicio a través de las tres tareas típicas de gestión de un negocio: tareas de resolución de problemas (del diseño al lanzamiento), tareas de gestión de la información (recepción de pedido hasta planificación de expedición) y tareas de transformación física (desde las materias primas hasta el producto terminado).
Hay que notar que en la producción lean, el flujo de la información es tan importante como el de material.
Todo mapa de cadena de valor debe comenzarse por el lado de las necesidades del cliente. A continuación, se plantean los procesos básicos de producción. Y en cada proceso hay que recopilar la siguiente información:
- Tiempo de ciclo.
- Tiempo de cambio.
- Número de trabajadores.
- Tiempo de trabajo disponible.
- Tiempo de funcionamiento.
El VSM de estado actual
No hay que perder de vista que el trabajo que se está realizando es la representación del mapa de flujo de valor (VSM) actual para localizar los desperdicios, que en una segunda fase buscaremos reducir.
Por lo tanto, a medida que se recorre el flujo de material actual se irán descubriendo los puntos de acumulación de inventario que deben quedar identificados en el mapa para ver dónde se detiene el flujo. Al acabar los procesos de transformación, se procede a representar la expedición de material y la recepción de este, incluyendo almacenes y cadencia.
Una vez terminado el mapa de flujo de material, se procederá al análisis y representación de los flujos de información diferenciando las diferentes vías, electrónica o papel.
Los procesos deben conectarse mediante reglas Pull, Push o FIFO para visualizar la forma en que el material pasa a través de estos:
- Push (empujar), en este sistema se fabrica con antelación. Por lo tanto, este modelo está directamente relacionado con la predicción de la demanda, ya que es indispensable saber previamente y con la máxima precisión qué productos requerirán los clientes, cuándo y en qué cantidad. Suele ser el procesado de grandes lotes a máxima velocidad para pasar al siguiente proceso o para almacenar. Se traduce en un sistema con mucho inventario.
- Pull (tirar), sistema que adapta la producción a la demanda efectiva, lo que significa que el producto se fabrica únicamente cuando se genera una venta, es decir, una vez que la compañía recibe la solicitud por parte del cliente, al que se le da una fecha de entrega determinada. En el mapa, no se fabrica nada en las actividades aguas arriba hasta que se requiere en las actividades aguas abajo. Al haber muy poco inventario, se genera un sistema ágil con mayor capacidad de respuesta a la demanda.
- FIFO, cuando el primer producto o componente a entrar en un proceso o ubicación de almacenaje, es también el primero en salir. De esta manera se evita que productos queden obsoletos o se oculten problemas de calidad con el inventario.
Finalmente, en el mapa obtenido se dibuja una línea de tiempos por debajo de las casillas de procesos y de los triángulos de inventario. En la parte superior se refleja el tiempo de inventario y en la parte inferior se refleja el tiempo de transformación, que es el que agrega valor añadido al producto. Sumando ambos se obtiene un indicador llamado Dock to Dock (DTD) o Tiempo Muelle a Muelle, que es el tiempo que tarda una pieza en recorrer todos los procesos y salir expedida. Si se comparan ambos, se obtiene el indicador Ratio de Valor Añadido (RVA), que da una idea del porcentaje de tiempo que realmente le está dando valor al producto. Estos dos son también indicadores típicos de la metodología Lean.
Ejemplo de mapa actual
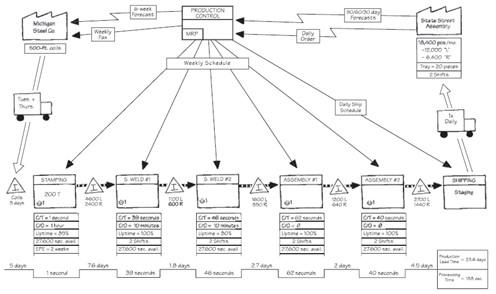
Obteniendo el VSM futuro
Como hemos adelantado, el siguiente paso es desarrollar el mapa futuro, para lo cual, de cara a conseguir una producción Lean, tendremos que eliminar las fuentes de desperdicio.
La otra característica de una manufactura Lean es la conexión de los procesos desde el consumidor final hasta la materia prima, mediante un flujo uniforme y recto con plazos de entrega más cortos, mejor calidad y al mínimo coste.
Con estos preceptos se establecen las siguientes reglas que nos ayudarán a configurar el mapa futuro:
- Adaptar la producción al Takt Time del cliente. Se define el Takt como la frecuencia con la que se debe fabricar una pieza o un producto en función del ritmo de ventas para satisfacer las necesidades del cliente. Se calcula el Takt del cliente como el tiempo de trabajo disponible por turno, dividido por el volumen de la demanda (en unidades) por turno.
- Crear un flujo continuo en la medida de que sea posible. Con flujo continuo nos referimos a una producción de piezas una a una, pasando de un proceso al siguiente sin paradas.
- Utilizar supermercados para controlar la producción. Regular la necesidad de producción por lotes mediante la creación de supermercados vinculados a las necesidades del proceso cliente y regulados con tarjetas Kanban.
- Insertar la programación del cliente en un solo proceso de producción. Se programará la producción en un solo punto de la cadena de valor cuando se recurre a flujo de material por supermercados. Este punto se llamará “marcapaso” al marcar el ritmo de todo el proceso anterior. La transferencia de material hacia adelante se hará en flujo continuo. De ahí que el proceso marcapaso sea el proceso de flujo continuo que está más atrás en la cadena de valor.
- Nivelar la combinación de la producción. Frente a la fabricación de grandes lotes durante periodos prolongados, se programarán fabricaciones cortas de todas las referencias en el proceso marcapasos buscando tiempos de respuesta cortos y una reducción de los almacenes intermedios. Por el contrario, se complica la producción con mayor número de cambios.
Nivelar el volumen de producción. Se trata de modular el ritmo dando órdenes frecuentes al proceso marcapasos y retirando el mismo volumen de producto terminado.
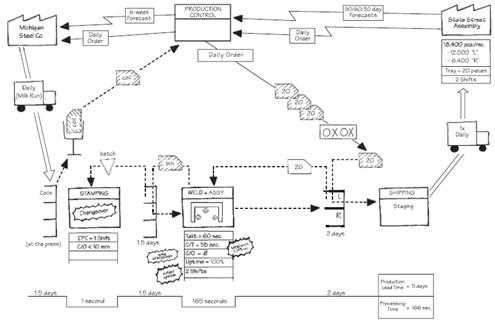
Al comparar el resultado de la línea de tiempos de ambos mapas, el actual y el futuro, vemos que el potencial de mejora es altísimo. Pero, por supuesto, el VSM futuro es una situación muy ambiciosa, de máximos. Cada industria deberá adaptarlo a sus posibilidades y graduar las mejoras con un plan de acciones.
Como siempre, si estás interesado en saber más o tienes un proyecto de mejora en tu empresa contacta con nosotros.
CADE, apoyando a la transformación de la industria.